How long are we going to hold on to obsolete concerns of the
past?
Over the last 30 years we have learned a tremendous amount about
how to design lightweight and reliable cooling systems. Through
racing experience we have found out how to properly cool high
performance engines. Today we use high precision manufacturing
technologies to cast and cut the parts that make up our engine
components – minimizing manufacturing flaws and making better
use of the base materials.
Back in the 1950's and even through the 1970's brass/copper radiators
where the norm. These radiators were both thermally inefficient
and were prone to cracking and leaking under vibration. Brass/copper
radiators are now a thing of the past. Aluminum radiators provide
much better thermal efficiency and are much more capable of withstanding
the vibrational environment of an aircraft installation. Where
a brass/copper radiator would barely be able to hold 20 psi of
pressure - today's aluminum radiators can withstand pressures
upwards of 50 to 90 psi without failure.
Myth - Air-cooled engines are very reliable
Do you really think that air cooled engines are that reliable?
Think again. There are far more catastrophic failures of air cooled
engines than you might care to admit.
As pilots, we are indoctrinated to believe that we are less likely
to suffer an engine failure than any other reason why we might
have to deal with an unscheduled landing. While statistically
speaking that may be true - statistics can also provide a false
sense of security. I'll venture a bet that you either (a) had
one of the following failures or (b) know someone that had one
of the following failures or (c) have a friend or acquaintance
that knows someone that had one of the following failures. If
you said yes to a, b or c above then statistically speaking there
is a 1 in 6 chance it could happen to you!
Consider the more common failures that are reported:
- Separation of the exhaust valve from the stem.
- Exhaust seat falling out of the head.
- Cylinder separation from the crankcase.
- Piston and/or piston pin failure.
- Broken rings - severe loss of compression failure.
- Some other top-end related engine failure.
These failures are almost all heat related. The tremendous heat
stress that the exhaust valve and seat are exposed to. The soft
metal that air-cooled heads are made of can barely retain the
exhaust valve seat at high temperatures. The detonation that most
likely contributes to the separation of cylinders from the crankcase.
All of these failures are massively catastrophic and have resulted
in the loss of life on many occasions.
Our company president with about 1000 hours flying time suffered
a catastrophic oil pump failure in July 1996 while flying behind
an O-360 Lycoming engine. Luckily he was able to land without
incident. Statistics would have you believe that such a failure
would be virtually impossible for someone to encounter with as
little as a 1000 hours of flying time. The reality is that the
oil pump failure suffered by our company's president along with
the other catastrophic failures listed above occur far more often
than the statistics would suggest.
The bottom line. We can hold on to obsolete concerns of the past
- or we can move forward - improving our engine's reliability
and even reducing the chances of catastrophic failure due to the
high operating temperatures of our air cooled engines.
"What if it springs a leak?"
The fact is, if the coolant system is properly maintained there
is a much lower possibility of a coolant system leak or failure
than an oil system leak or failure. Consider that the oil system
in an aircraft engine must be capable of handling what is essentially
a corrosive and highly viscous fluid at high pressure. The oil
pump in an engine is subject to extreme stress when the engine
is started cold. Why? Because it must pump a very viscous fluid
at high pressure. The forces and horsepower required are very
high. Oil pump failures are far from uncommon. Likewise oil
coolers must be designed to withstand the higher pressures of
the oil system and of course lets not forget the hoses and fittings
between the engine and the oil cooler.
Are you thinking about your car's cooling system? Soft rubber
hoses and hose clamps that tend to loosen up? Fan belts that break
at the most inopportune times? Well don't even compare your car's
cooling system to what we have designed for our Cool Jugs' cooling
system. Our goal has been to design a system that is more reliable
than the engine's oil system.
Our company president - who is also the Chief Engineer and Test
Pilot for the water cooled conversion project provided the basis
for the design. He said, "I want to feel confident flying
a water cooled single engine aircraft over the Mojave desert
on a cold dark night, under a high overcast without a star
in the sky"
To meet that requirement we use only well established aviation
grade design techniques and hardware. For example, the coolant
hose kit for the Cool Jugs conversion utilizes AN fittings,
and steel reinforced synthetic compound hoses with a 500psi
burst rating that are fully aviation certified TSO C53a. That's
a burst rating that is over 25 times the operating pressure
of the cooling system!
Our coolant pump is the essence of simplicity and reliability
- designed to last at least 10,000 hours it is gear driven directly
by the accessory drive with one moving part that does not come
in contact with anything other than the coolant. A long life
ceramic water seal prevents any leaks.
As for servicability - the pump can be overhauled with a pair of
snap ring pliers and a light press. Our coolant manifold is constructed of 6160-T6 aluminum components
and is designed to not suffer any fatigue as the result of thermal
expansion and torque flex that occurs during engine operation.
Finally - we worked with mother nature! Yes, we designed our
cooling system to have a natural convective flow so that even
in the highly unlikely event of a cooling pump failure the system
would still be able to keep the engine temperature under control.
The natural convective circulation is so effective that it will
continue to cool the engine while it is running at power levels
up to 30% without the coolant pump operating! While 30% may
not sustain level flight in many aircraft it will considerably
extend the glide performance and will allow the engine to be
operated at maximum power in short bursts as necessary to execute
a safe landing.
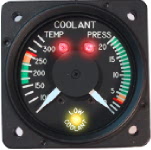 |
Even with all of the effort we put into designing a leak
proof and reliable cooling system we went one step further
- we designed and built a sophisticated cooling system analyzer
that will provide the earliest possible warning of a cooling
system issue before it becomes a critical problem. Our cooling
system analyzer provides a complete picture of the condition
of the cooling system and can provide a warning when as little
as 8 fl.oz. of coolant is lost from a 2.5 gallon system
- long before there would be any urgency. It uses technology
and methods that are so unique that we were awarded US Patent
#7,069,883 on July 4th, 2006. |
Ease of Maintenance
Every aspect of the Cool Jugs conversion has been designed to
allow ease of engine maintenance. We have made sure that the system
is entirely 'bolt on' with all components easily accessible for
inspection and maintenance. We have eliminated virtually all gaskets
and replaced them with 'O' rings that provide a more reliable
seal and are less prone to leakage.
The only recurring maintenance that we require is that the system
thermostat and the coolant be changed at every 3rd annual inspection
or 1000 hours of operation, whichever occurs first. Over time
we will likely extend the change interval as we gather more
long term data.
Put you mind at ease...
Be assured by these facts!
- Highest Quality Aviation Components
- Minimal Changes to Base Engine
- No Changes to Any Internal Parts
- Modular Design Utilizing a Minimal Number of Unique
Parts
- High Performance Gear Driven Coolant Pump
- Precision Made Parts Using the Latest Casting & CNC
Technologies
- Strong, Reliable & Light Weight Components
|
|